MTAC Team members work together in a variety of high-risk, heavy production projects for a wide variety of clients in a vast collection of site settings. While at our facility in Plainfield Indiana, on Indy’s west side producing Healthy Barriers or doing some custom fabrication work, we are all focused on bringing the best we have to offer to the effort we are working on. Whether we are working in the stifling heat of a warehouse over 30 feet up in the air replacing burnt-out light bulbs or kneeling beside a damaged pallet rack frame in a sub-zero freezer, we face every adversity as a team.
“Each one of our technicians has been trained in the services we perform, and each is certified to use the equipment we bring to bear on the tasks we tackle.”
Troubleshooting, diagnosing, fact-finding our challenges is a daily walk for our group and we all take pride in bringing our best game to the challenge. (We think of ourselves as modern-day minutemen and women!) At any point of the day (or night) we might get a phone call, a text message, or an email from one of our valuable clients, seeking our assistance in sorting out a problem they are facing that is about to threaten- or, worse yet, has actually stopped- their efforts to do what they do. And that’s where we shine!
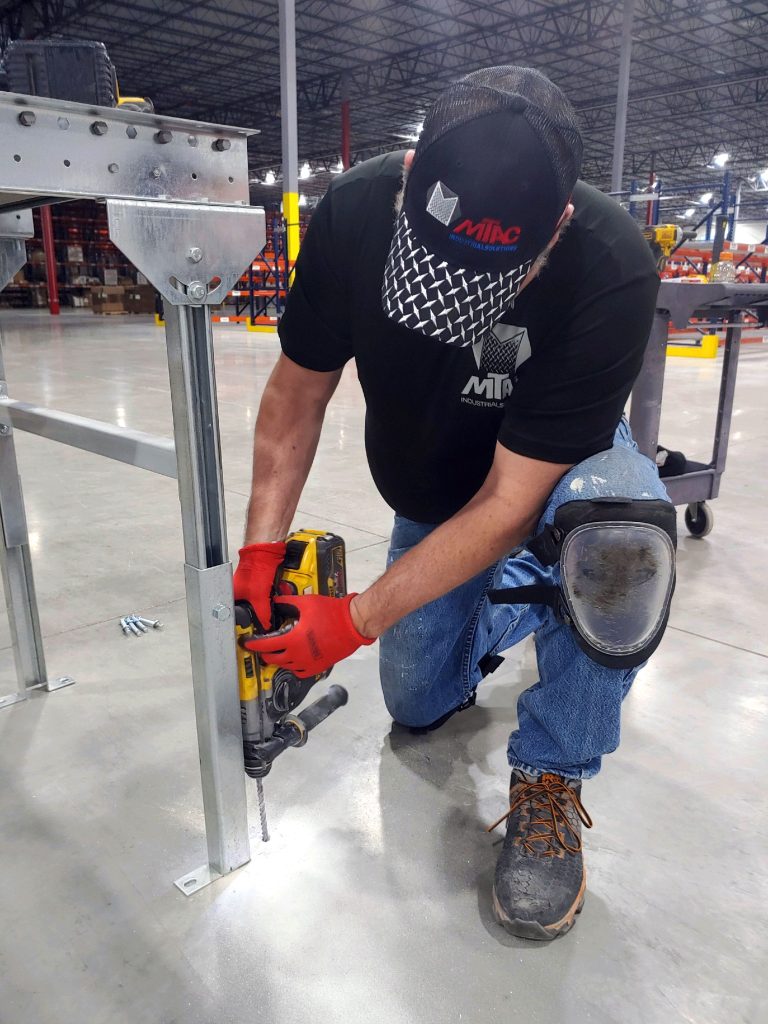
Getting the Job Done
Our Field Operations Manager Bryan Alexander has a can-do attitude that customers love when they need something done in a timely manner. Our Operations Manager Taylor A Bruckerhoff has recently returned to our team and has a remarkable ability to balance our in-house production/manufacturing efforts with our local and national commitments. These two guys have a solid working relationship and just a few minutes with them is all it takes to understand they know their work and enjoy doing it. It probably helps that they both like to spend time with their families camping and roaming the great outdoors. But when they are at work, it’s all business!
Bryan ran a successful company of his own for over 25 years before joining our team. He has contributed a lot to our team and we appreciate his easy management style balanced by his drive to get the job done right.
Taylor worked for us for several years as our lead technician before going off to follow his dream job as an airplane mechanic. He worked hard for our clients by day and then spent his nights going to school to get his A&P Certification so he could service aircraft. He landed a good job but when COVID impacted the airline industry so thoroughly in early 2020, he understood his job was threatened through no fault of his own. We talked and he offered to return to MTAC and I was pleased to welcome him back to our team. Taylor now manages our team and I couldn’t be prouder of his transition from technician to manager. Big T and Bryan are doing a great job for me, and I am looking forward to the day when you call and I can unleash this dynamic duo on your challenges. They make it look easy!
Behind the Scenes
Jen Poynter and Taylor B. Bruckerhoff tag-team to keep up with the tsunami of receipts, expenses, invoices, and payroll for this growing company. Our staff doubled in 2020 alone! You can imagine the work it takes to keep up with a growing crew of industrial service technicians and all of the work they are accomplishing in addition to staying on top of all of the AP, AR and payroll details.
With 2020 and the COVID concerns, we morphed into a full time manufacturing company in addition to being an installation and service group. (This is very much like having 2 companies under the same roof.) One group shows up at our customers’ sites when they need us most to maintain or improve their facility, while the other group is steadily working away at producing world class industrial grade barriers to satisfy our customers social distancing requirements.
Now, wrap your head around the fact that there are just 2 very talented and capable gals in the office keeping up with all of this activity. Jen has a strong background in administrative assistance and HR, and Tay has education and experience in the administrative side of the medical field. When her husband decided to return to MTAC to take on the Operations role, she decided to join our effort and made the switch from the medical to the industrial sector (and made the transition look easy!) Jen and Tay get along like mother and daughter with good reason- they are! It is so cool watching these two working side-by-side as they combine their respective skill sets to effectively accomplish what would otherwise take a full team of office staff to keep up with.
Industrial Solutions
Our Industrial Solutions Specialists, Jon Poynter, and Stefan Navarrette, are both men of experience and each has honed their skills at troubleshooting, damage assessment, and problem solving to a level that is truly something to respect. Jon comes from a strong fabrication and machine programming background and his skills have dovetailed well with our drive to not just participate in the Healthy Barriers sector, but to truly set the pace for the marketplace and to help elevate it. With an eye for quality and a passion to get it done right the first time, Jon is a glove fit for our team.
Stefan has a unique ability to catch on to what is going on (and in some instances, what isn’t happening) quickly and accurately. Like Jon, he can evaluate the damage to the systems we maintain for our clients with intense scrutiny and then provide the correct solution for the application. He is already performing like a veteran of our field and I can’t wait to see what he does as he continues to develop his craft.
Both of these men are the right guys at the right time to help MTAC Industrial Solutions help our clients with their most pressing needs. Jon and Stefan are regularly working to solve problems with using Healthy Barriers one day and then pivoting to damaged pallet rack structures the next day. They are both just as comfortable as I am putting on a tool belt and getting to massive production efforts to help meet our deadlines. They both understand that work means changing something from what it was when you arrived to what someone else needs it to be before you leave. That doesn’t “just happen”- it takes planning and follow-through. That’s who we are and that’s who they are.
Our Technicians
MTAC technicians are more than just our hands and feet when it comes to getting your jobs done. This group is sharp! They all catch on so quickly to the changing landscapes we routinely encounter as we churn through the work week.
By name: Brian Jones, Michael DeWees, Jordan Parker, Rick Johanningsmeier, Matt Neuman, Joe Sisk, Christian Alexander, and my son, Ryan Klinger, all work together as a single unit when it is time to knock out the jobs we take on. An admirer recently stated: “Yeah, those guys do manly work, they lift boulders!” That cracked me up when I heard it, but it’s true. WE LOVE the challenges we are constantly facing, and this team of technicians is all about getting to the bottom of it and getting it done. They each embrace the axiom that the company was actually founded on: “Don’t just get it done…Get it done right!” It was what got me out of bed when all of this started, and it is what gets them out of bed today.
We all recognize there are others who can do this work; we are not unique. But there truly aren’t many who do it the way we do. Pride in ownership still means something here. Each of these men and women enjoy the satisfaction we get from a hard day’s work. It’s ok to get dirty, work up a sweat, and even get exhausted trying to get through the next job, but this crew doesn’t cower from that sort of effort- they enjoy it and excel at it! (Try to find that kind of commitment in today’s workplace; it’s a dying art.)
When I was a young man, a person who could perform with skill in a variety of trades and tasks was a dime a dozen. Today you can look for weeks and never find that caliber of person. You have to look under a lot of rocks to find motivated people who want to deliver what was sold, without cutting corners or doing the task ‘half-vast’. Look no further: you have found them here at MTAC Industrial Solutions, and we are looking forward to seeing how we can help you next.
Our technicians love installing new goods in new spaces, they love returning to maintain them for you, AND they ABSOLUTELY love having to think outside the box to find the shortest path to getting you back-up-and-running! Every member of our team has been trained in the MTAC school of working to solution because we are a solutions-driven company.
- What is broken, not working, or otherwise not producing?
- What do I have here to meet the challenge?
- What tools, materials, resources are at my fingertips to solve this problem?
- What is the customer’s expectation?
- What’s the budget, the downtime, and the period of time needed until everything is back to “normal” and the problem is solved?
- How about the lost time calculations, and the cost to the customer?
All of this encompasses our intense motivation to deliver. Within all of these variables and considerations, we work overtime to provide options, recommendations, and above all, Solutions!